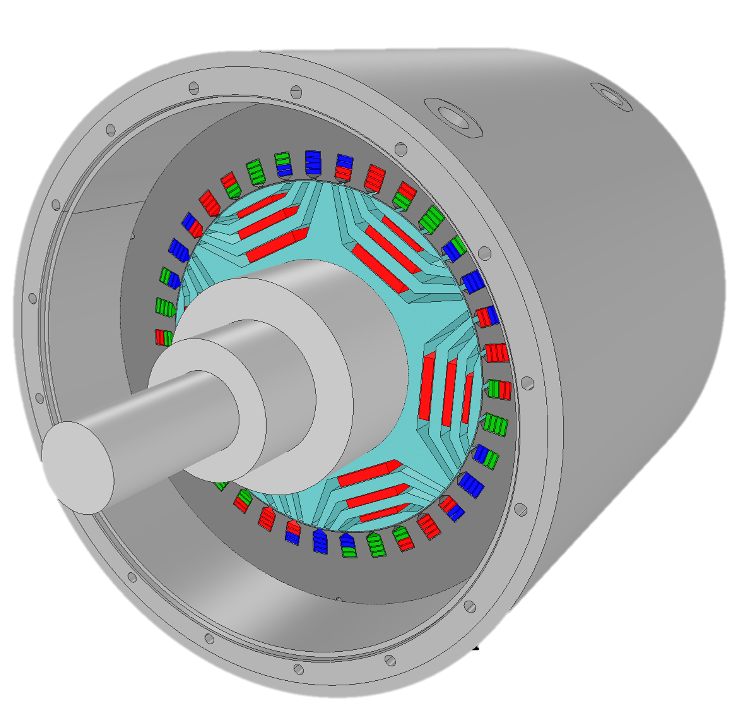
ReMoS 2 - Effective Reluctance Machine for Emission-free Mobility without Rare Earth Materials
- Contact:
- Project Group:
Hybrid Electrical Vehicles
- Funding:
Innovationscampus Mobilität der Zukunft (ICM)
Total project funding: ~ 550.000 € - Partner:
Institute of Vehicle System Technology – Division Lightweight Technology (FAST-LBT) – KIT,
Institute of Engineering and Computational Mechanics (ITM) – University of Stuttgart
- Startdate:
01.01.2022
- Enddate:
24.12.2023
Objectives and Results
In the preceding project a new machine concept with the goal of improving the efficiency of the synchronous reluctance machine (SynRM) and the permanent magnet assisted SynRM was presented. This concept aims to deal with the conflicting goals of optimal electromagnetic utilization and mechanical speed strength of the machine’s rotor by injecting the flux barriers with fiber reinforced polymer and applying rare earth free magnets. By doing so, the maximum efficiency is improved and higher maximum speeds are enabled. In the second phase – remos2 – the assembly of prototypes is planned. As part of this process the assumptions made about the interfacial strength between the electrical sheets and the polymer need be investigated experimentally and the rotor geometry must be adjusted accordingly. Furthermore, the tools for mould injecting the polymer into the flux barriers will be designed and the rotor and stator concepts are to validated through prototypes and measurements.
Contents and Approach
The improved efficiency under partial load in field weakening operation is validated with a machine prototype. Using adhesive and peel tests, the simulated elevation of maximum rotor speed is quantified by evaluating the maximum permissible contact forces. Furthermore, the injection moulding process necessary for the production of the prototypes is simulated in detail, and from this basis an injection moulding tool is designed and built.
The change in magnetisation in the rotor during operation presents a control engineering challenge. Control strategies are to be designed to overcome this challenge and achieve optimised overall efficiency in driving cycles. Additionally, the effect of skewing the rotor on the remagnetisation process is to be investigated.
The NVH behaviour of the machine is affected by the variable magnetisation as well, because the changed magnetisation creates an additional degree of freedom in the noise excitation. With a model already developed for fast analyses of the NVH behaviour under transient conditions the final designed machine can be examined and a final validation be performed on the test bench.